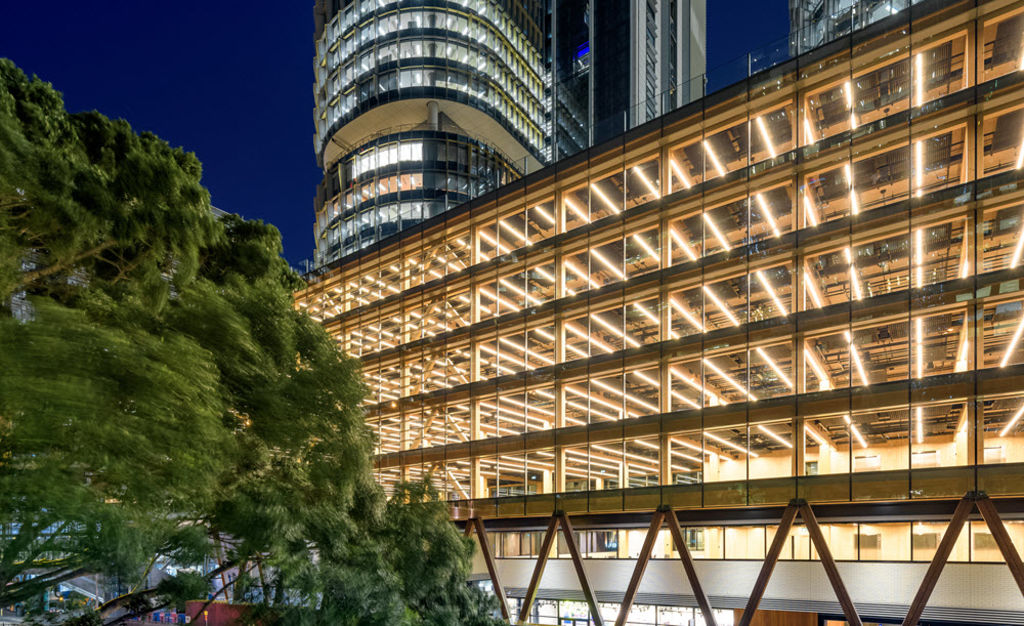
Australia to become self sufficient in engineered timber by 2020
“What,” asks Sydney architect James Fitzpatrick, “has our generation added to new technology and ways of building?”
Since the 1970s, argues the founder of Fitzpatrick + Partners, “nothing substantial has been added to the architectural oeuvre.
“But suddenly there is a technology and material that is of our time. So what we will leave, I think, will be engineered timber construction”.
With several Fitzpatrick-authored CLT (or Cross Laminated Timber) buildings already up – including his own home – and with a decade-deep investment in researching the scope of the various engineered timber products, Fitzpatrick is a passionate promoter of a sustainable and beautiful building material that has, to this point, been largely sourced from Europe.
But courtesy of two new Australian-based manufacturing plants – one that commenced construction on Thursday, January 17, in Maryborough, Queensland – by the end of the year Australia should be able to supply its own needs for what is already termed “the GLT (Glue Laminated) Revolution”.
Hyne Timber, a multi-generational business established in Queensland in 1882, is investing $20 million in a major GLT plant which is expected to come on line by mid 2019.
Hyne’s strategic relations manager, Katherine Fowden, credits on-shore demand for stimulating this and another large plant opened by the company XLam, in Wodonga, to produce engineered timber panels. Both resulted “from an incredible pull in terms of (local) demand for the products”, she said.
More expansion plans are underway, she said, but already the buzz around these on-shore plants was “the talk of the construction industry”. And all this while there are only a dozen or so engineered timber buildings around Australia that you can actually walk into.
Five of them, including the internationally lauded “International House” at Barangaroo, and the much mooted “25 King” – which opened in the regenerating part of Bowen Hills, Brisbane, in November “as Australia’s tallest engineered timber tower” (at nine levels) – have been built by Lendlease.
The company currently has its sixth CLT structure in the pipeline. “Damaru”, which in the Eora Aboriginal language of the Sydney region means ”treehouse”, will also be at Barangaroo and will rise to six levels.
This smattering of structures, said James Fitzpatrick, was the work of “the early adopters”. Yet, he believed, because each new engineered timber structure “has added its own complexity and gone off in its own direction, they have added much to the library, because each has really pushed the boundaries”.
Among the engineered timber buildings Fitzpatrick + Partners has realised is Strongbuild’s head office at Bella Vista, in Sydney. It has another six on the drawing board including a 16-level office building. As a purely theoretical exercise, the studio is presently researching the feasibility of a 100-storey GLT structure that, Fitzpatrick admits, “won’t happen in my lifetime but is a way of looking at the possibilities of the materials”.
Gauging by what’s happening overseas, the sky is the limit for products that appear to symbolise a seismic shift in 21st-century design and construction.
In Stockholm, for instance, master planning has been undertaken for a 5000-residence precinct comprising 31 GLT towers. In Tokyo there is a proposal by a big timber company for a 350-metre-high timber skyscraper.
Canada, Finland, the Netherlands, New Zealand and Tasmania, have all endorsed “timber first” or Wood Encouragement Policies (WEP) to push lightweight, sustainable, recyclable products that offer a 40 per cent energy saving over the same amount of steel, and that Fitzpatrick agreed was so attractive “as a beautiful material that addresses all the environmental issues but that is also highly accurate.
“Prefabricated in a factory using computer technology, we are suddenly working with tolerances of 2 millimetres, so everything comes together cleaner and neater – and more safely and cheaply.”
And much more aesthetically? “Well”, he said, “No-one asks you to come around to look at their aluminium windows, do they? But they might talk about their lovely wooden ones.”