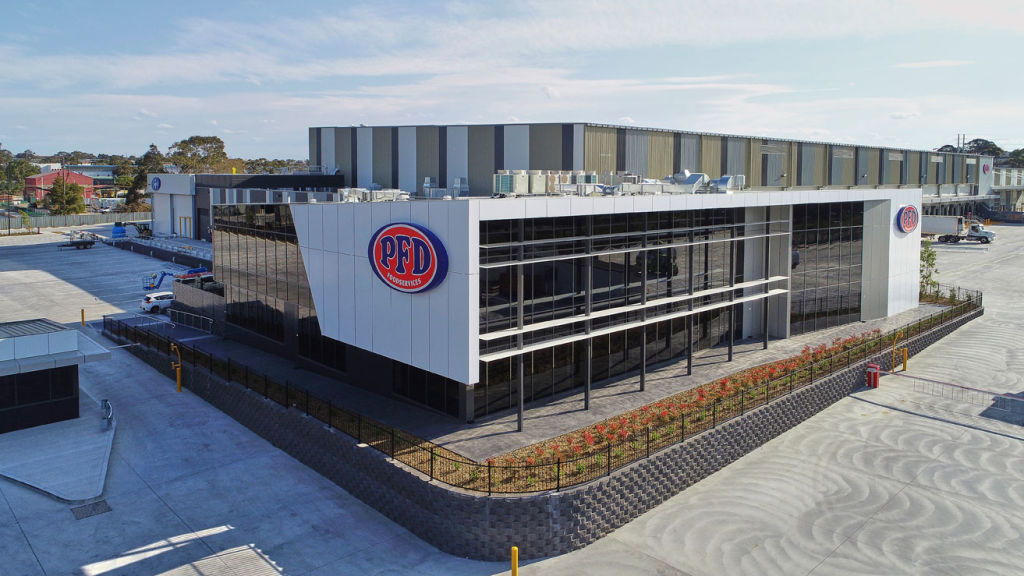
How warehouses are going green and saving money through water harvesting
Industrial properties are following in the footsteps of the office sector and incorporating sustainability initiatives, with water harvesting at the centre of these efforts.
While sheds and factories might not seem like the type of real estate with significant sustainability potential, water harvesting is sought after by industrial property owners and users, according to Travis Erridge, cofounder and director of TM Insight.
“Five years ago, water harvesting was limited to tier-one builders and developers, but it is now ubiquitous for any new facility over 10,000 square metres,” he said.
“Demand is growing due to the commercial benefits for tenants and also the ability to reduce their environmental footprint, which is an important issue for many companies from a corporate governance and corporate social responsibility lens.”
In regular industrial sites, water harvesting, which captures and stores rainwater from a building’s rooftop to use as an alternative source of water, is generally used for landscaping irrigation and toilets.
But for refrigerated industrial facilities, such as frozen and chilled food storage, water harvesting is becoming a crucial part of its strategy to be more resourceful with its water consumption and create operational savings.
“In a refrigerated environment, water is used across the condensers to create cool air. During hot days, a large amount of water is needed to keep the environment cool. Tenants are using harvested water to generate the large amount of water required, which is saving a huge amount of main water and also water costs,” Mr Erridge said.
He noted that the benefits and savings of water harvesting can be maximised if used with solar power.
“This is due to the fact that hot days are when refrigerated warehouses need to draw the most amount of water for condensers and also a large amount of power to run the fans to keep the temperature cool,” he said.
While an average water tank is priced at about $200,000, Mr Erridge said that the system could pay itself back within one year for an occupier if the landlord rentalises the cost of the system with the base building.
The cost is rentalised, or added to the agreed property rent, at about 6 per cent to cover the charges, which is effectively paid off by savings on water costs.
But this only applies if the water harvesting system is considered in the design phase of a building and is rentalised from the developer.
Mr Erridge pointed out that even for a non-manufacturing or cold storage facility, the commercial benefits of water harvesting are worth considering.
“For a more typical warehousing occupier, such as a retail or FMCG (fast-moving consumer goods) business, cost benefits are less pronounced, but it is the compounding benefit (that is key) if rolled out across the assets of industrial landlords/developers such as Frasers Property, Goodman, Charter Hall and Dexus,” he said.
Mr Erridge believes that by having a feature that creates value for tenants, the properties’ appeal and value will increase.
Surging demand from tenants
PFD Food Services, which distributes food products for big names such as Kraft, Inghams, Fonterra and Mars, is one business that has included water harvesting in its facilities at Sydney’s Chullora and Melbourne’s Knoxfield.
Kerry Smith, chief executive officer of PFD Food Services, said it was important for the company to incorporate water harvesting systems as part of their corporate social responsibility and sustainability guidelines, while increasing efficiencies within the building.
“The water harvesting system is part of the base building costs and rentalised back to us, so value for us is realised in the first year of operations with instant impact to our sustainability,” she said.
“The use of water harvesting at our facility has allowed us to be more environmentally responsible with our practices and save on water costs, which creates greater operational efficiencies in our business.”
And according to industrial property developers, tenant awareness of and demand for water harvesting systems is on the rise.
“Over the last few years we have seen an evolution of requests starting from a rainwater tank itself, to the use of the rainwater for landscape irrigation and more recently, toilet flushing and truck wash,” Frasers Property’s sustainability manager for commercial & industrial Andrew Thai said.
Water harvesting is already a common design element in new industrial facilities, Mr Thai said, but he still expects the movement to evolve.
“What will trend is the use of the collected water for things other than landscape irrigation. These would include toilet flushing, truck wash and even for water-based air conditioning systems,” he said.
Richard Seddon, general manager for industrial at Mirvac – which in May opened its newest industrial estate Calibre in Sydney’s Eastern Creek – said he was seeing a “noticeable improvement in the awareness and benefits of sustainability measures” across the industry.
“Customers will always seek ways to derive operational savings, and rainwater harvesting can help contribute to this,” he said.
“At Calibre there is over 100,000 square metres of roof space, we have capitalised on this opportunity by incorporating rainwater harvesting and re-use on each building.”
Mr Seddon agreed that water harvesting would become more widespread.
“It should become standard practice for future industrial properties as it is a natural opportunity given the typically large-format nature of these buildings,” he said.